
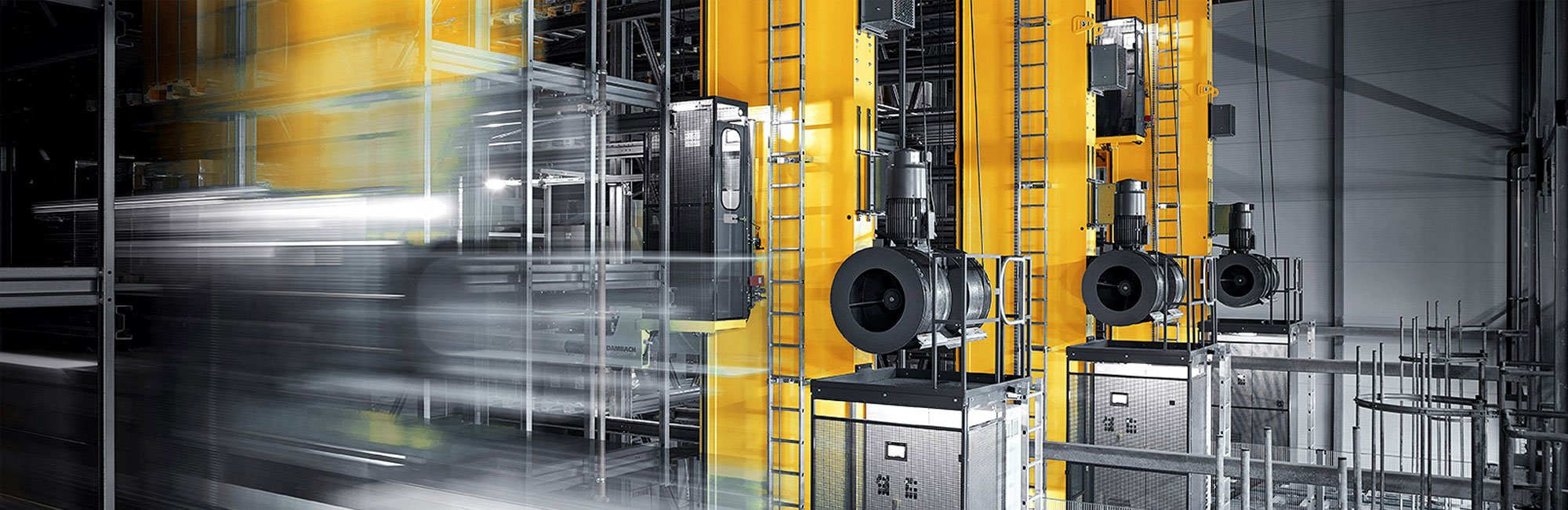
The weight of the cell-goods carriers thereby varies between 25 and 100 kg total weight per position. For large battery cell storage areas, this can lead to repositioning times of 2 - 5 seconds per unit in a warehouse. The cells must be repositioned frequently, depending on the measured cell performance results. DAMBACH makes use of highly dynamic telescopic tables for aging racks with support bases. Temperature ranges of up to 50 ☌ place increased demands on the control system and electronics.
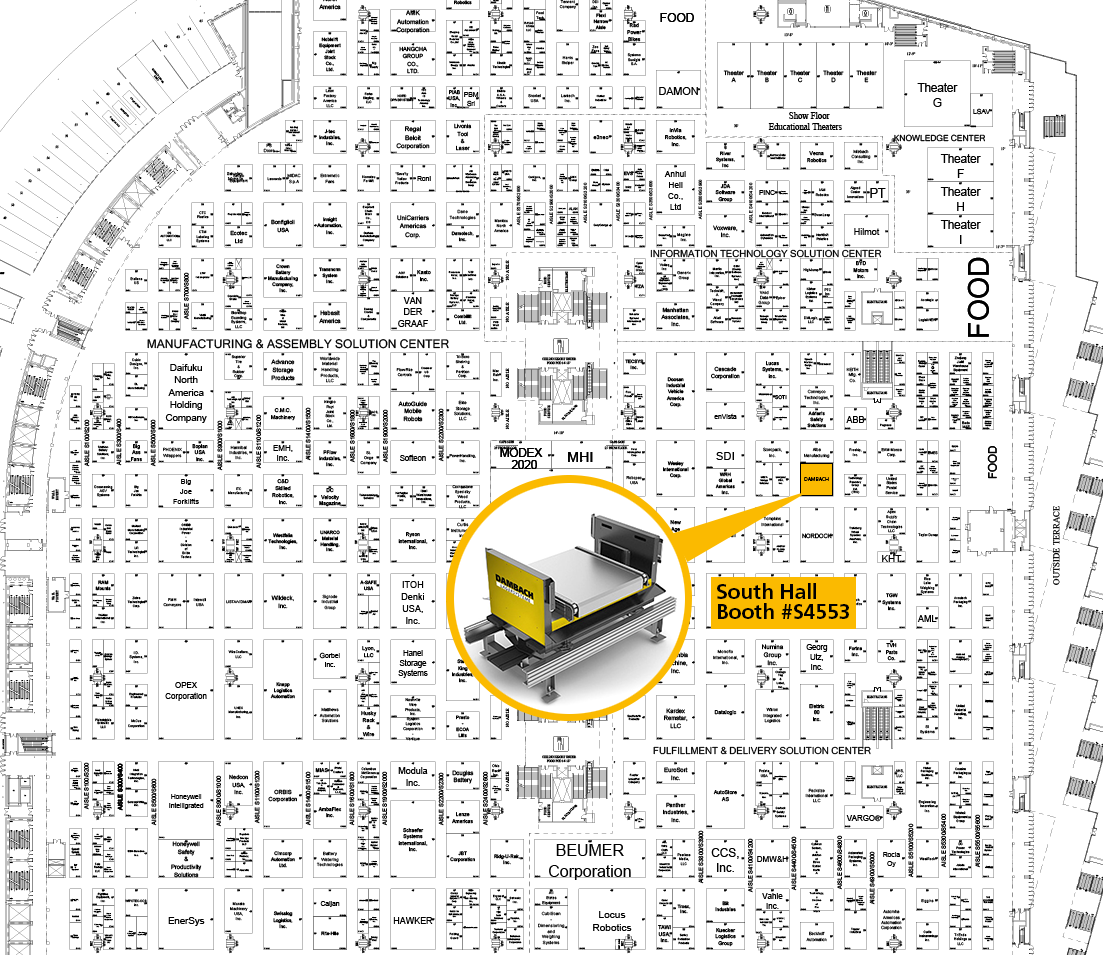
Various aging stages during cell assembly lead to further storage system requirements. Exact battery cell positioning below the charging pins in storage is of great importance for successful charging and discharging during formation. With its coordinated load handling attachments, DAMBACH ensures a combination of form- and frictional locking during storage and removal in special formation racks. The first priority thereby is the safe handling of the cells. Additionally, differing geometries for cylindrical, prismatic, or pouch cells lead to different cell load carrier dimensions.īattery cell load carriers may need to be stacked, stored in high-rack storage by means of push-pull grippers, or transferred to conveyor technology with telescopic forks for repositioning. Various storage and retrieval machines (SRM) or cross-transfer cars (CTC) with lifts are put to use, depending on the type of storage.Ī variety of small load carriers are used, depending on the manufacturing process for the battery systems and the cell type. DAMBACH storage technology thereby fulfills the high demands of handling capacity, storage density, and fire prevention concepts. A number of factors must be considered for reliable handling and efficient intermediate storage of these modern battery systems. Due to their high energy density, battery systems with lithium-ion batteries are currently one of the preferred energy storage systems in electric vehicles. Reliable and simultaneously cost-effective implementation of new intralogistics processes will be decisive in the success of electric mobility.Īutomated high-rack storage systems are playing an increasingly critical role in the area of cell production and battery storage. Even though this leads to a reduction in the variety of parts in the supply chain on the one hand, it also increases the complexity when handling battery components, which are mostly produced automatically and are subject to strict safety requirements. While a traditional combustion engine comprises more than 1,000 parts, there remain only about 20 components in an electric motor. These changes are influencing the entire automobile supply chain – including system suppliers of intralogistics solutions.
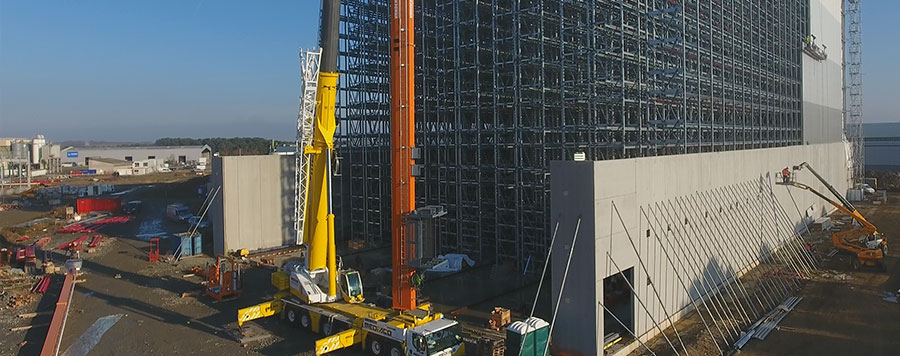
Value added chains and logistics concepts must be adapted to requirements that have changed in the automobile sector. Mixed production approaches for gasoline, diesel, hybrid and electric vehicles on a production line represent new challenges. For manufacturers, ambitious E-auto strategies are leading to rethinking production and storage concepts. As a result of market conditions and new climate goals, there is a growing reliance on electric mobility on the part of automobile manufacturers and automotive suppliers.
